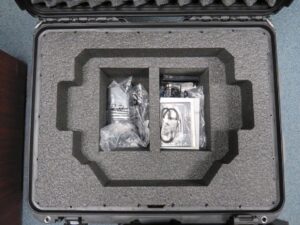
Injection molded cases provide you with the precise security and professionalism you desire.
Molding processes are essential for creating custom protective cases for numerous industries. People in the medical, military, and telecommunications field, for example, rely on custom molded cases, many times with custom foam inserts added, to carry and protect their valuable equipment from damage and misplacement when performing their work. One way to create custom cases is through injection molding. Injection molding is a quick and repeatable process, bringing several advantages to protective transit cases. If you are ready to explore available injection molded cases at Packaging Strategies, keep reading to discover why these custom cases are a worthwhile investment.
The Ability to Mold Complex Shapes
Highly precise and detailed tooling makes it possible to incorporate complex features and shapes into your injection molded cases. For instance, you can add reinforcing ribs exactly where needed to maximize strength and rigidity. Or, “O” ring grooves can be molded-in to provide optimal sealing when the case is closed. Your case can look precisely how you prefer when it is built through injection molding.
The Freedom to Optimize Material Properties
Your transport case isn’t very useful to you if it is easily damaged. The plastic resin used for these cases must provide consistent strength and rigidity. To ensure the case meets your expectations, a few companies such as SKB, Pelican and Nanuk use specific elastomers which create a more robust and impact resistant product. During the injection mold process, many parameters can be managed to optimize the way material flows and takes up the shape of the case cavity. These parameters can be controlled to create the highly durable case you need, made with your specific work conditions in mind.
Inject Molded Cases Have an Impressive Appearance
Inject molded cases are not only designed to protect professional gear and equipment but are intended to look professional and high-quality at all times. Whether you are a professional medic, videographer, soldier, or government employee, you want the cases that carry your equipment to reflect the professionalism you bring to the job. The polished appearance of molded cases creates a smooth, business-like finish that conveys to others that you take your responsibilities very seriously.
A Cost-Effective Process
Injection molding is a very efficient process, as little material is wasted during processing. If a case fails the inspection process then it can be shredded and reused again to make another case. So there is virtually no waste. Plus, the ability to recycle plastic cases after you are finished with them means that the material can be reused in the future. Additionally, with one press, hundreds of parts can be created. The parts can be identical or unique, but the production time is significantly shorter than other manufacturing methods. Injection molding is ideal for creating many parts in a short amount of time, which makes the process very cost-effective. No quality is lost during this production process, so you can feel confident in the durability and specificity of your new cases.
DEPEND ON PACKAGING STRATEGIES FOR YOUR CUSTOM PACKAGING NEEDS
Packaging Strategies has assembled a team with over 80 years of experience in design, engineering, development, manufacturing, and sales. We created the Packaging Strategies Design and Technology Center to create and manufacture complete systems integration packages and container solutions of all sizes and materials for our clientele. Many of these clients are federal agencies or in the private sector. No matter what you need to carry, Packaging Strategies is sure to have the right case for the job. You can view our website here, and follow us on Facebook, Twitter, Flickr, and Linkedin.
This entry was posted on Tuesday, October 18th, 2022 at 10:48 am. You can follow any responses to this entry through the RSS 2.0 feed. You can leave a response, or trackback from your own site.